I spent 11 years in fashion manufacturing – first as a cutting room manager, and eventually as a production director. In that time, I estimate that I must have touched tens of thousands of different fabrics, getting first-hand, tactile feel for how they would perform and drape in finished products. Back then, we used our senses as our primary guides; the Yiddish word “schmatta” (for “rag”) was what we uttered when we touched or eyeballed a low-quality fabric, and we knew instinctively that the material was bad without having to get into detail about its composition.
As fashion rushes headlong to embrace 3D, it’s going to be vital that we replicate that same ability to judge a fabric based on its look, feel, and performance. This is going to rely on digital materials that inherit all the important characteristics from their real counterparts. And this is also a vital part of how 3D vendors should communicate with retailers, brands, and manufacturers – emphasising the idea that what they see virtually is an accurate representation.
I would not class myself as any kind of expert or scholar when it comes to the physics of textiles, but I have spent a lot of time in and around both real and digital materials – with 35 years’ experience in 3D for footwear and apparel – and in that time I’ve learned several things that I believe are going to be absolutely key as the industry moves from draping physical fabrics to simulating the drape of virtual ones.
It’s truly amazing what can be achieved by using 3D today, whether it’s downstream towards the consumer, delivering virtual photorealistic twins, or upstream, following from product design and development through to manufacturing. The output of 3D can be made photorealistic and believable with greater ease than ever before.
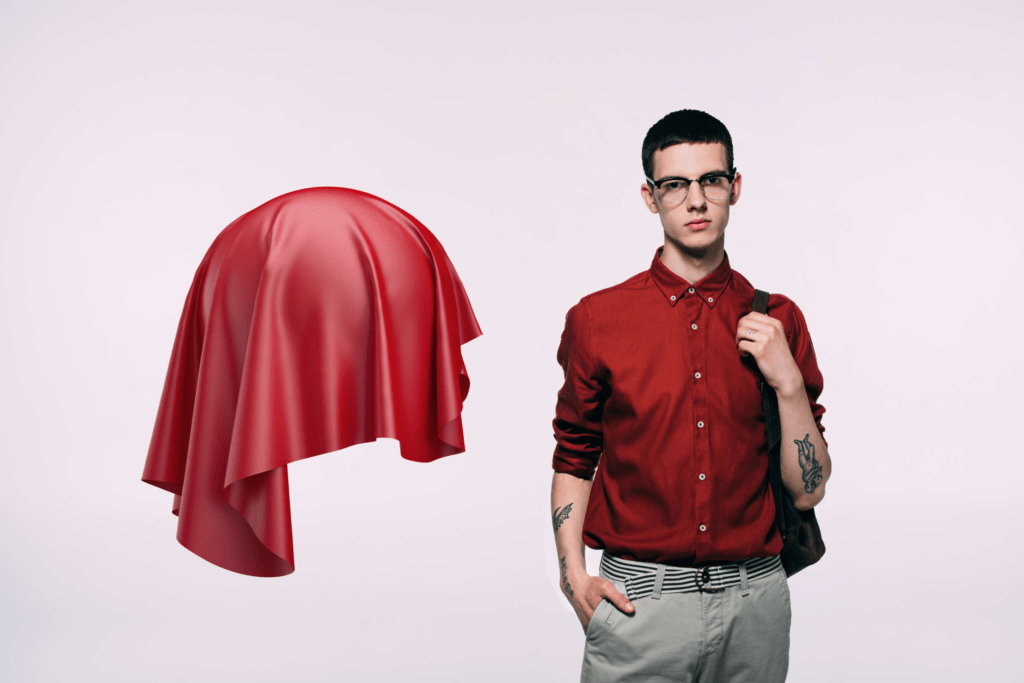
However a word of caution: 3D solutions can also produce virtual products that look real, but are actually physically incorrect and cannot be manufactured to the expected standard. For example, you might place a digital material onto your avatar and change the pattern piece angle by several degrees off the grainline and not see any visual effect upon the seam in simulation. If this was in the real world the seam, when sewn, would show puckering – and to remove the puckering you would need to realign the pattern piece back onto the grainline.
Now, before the pattern and sample makers among you comment: yes, you might get away with 1-3 degrees without puckering, but there is always a risk of compromising the quality of the finished product – something that increases the further that angle changes. This is why we need to precisely replicate the physics of materials into our 3D solutions: to ensure that the virtual is a near real-life representation of the physical.
If your business is considering a move towards a 3D workflow, then I would strongly recommend undertaking your own research into the technicalities of how virtual materials are simulated and what parameters govern the way they behave. Everyone – me included – wishes it was as straightforward as simply scanning a physical material and having absolute accuracy guaranteed, but like any other part of digital transformation, getting digital materials right involves careful planning.
Consider how many different characteristics need to be factored into 3D simulation for it to approach accuracy to the original physical material:
- Composition details, including cotton, silk, wool, polyester etc.
- Woven or Knits
- Material sheerness
- Bending properties
- Rigidity
- Firmness
- Tensility
- Thickness
- Weight
- Stretch
- Recovery
- Material finishing
I could go on, but I’m sure you see where this is heading. Every material, of course, needs to have its own set of these characteristics – and each of them needs to be individually imported, tested, and added to a centralised material library so that, whatever fabric the user chooses to drape virtually, the result will be as close as possible to real life. Moving forward these same material characteristics should also be added to material platforms as a standard, otherwise my concern is that we are adding unnecessary processes after the event!
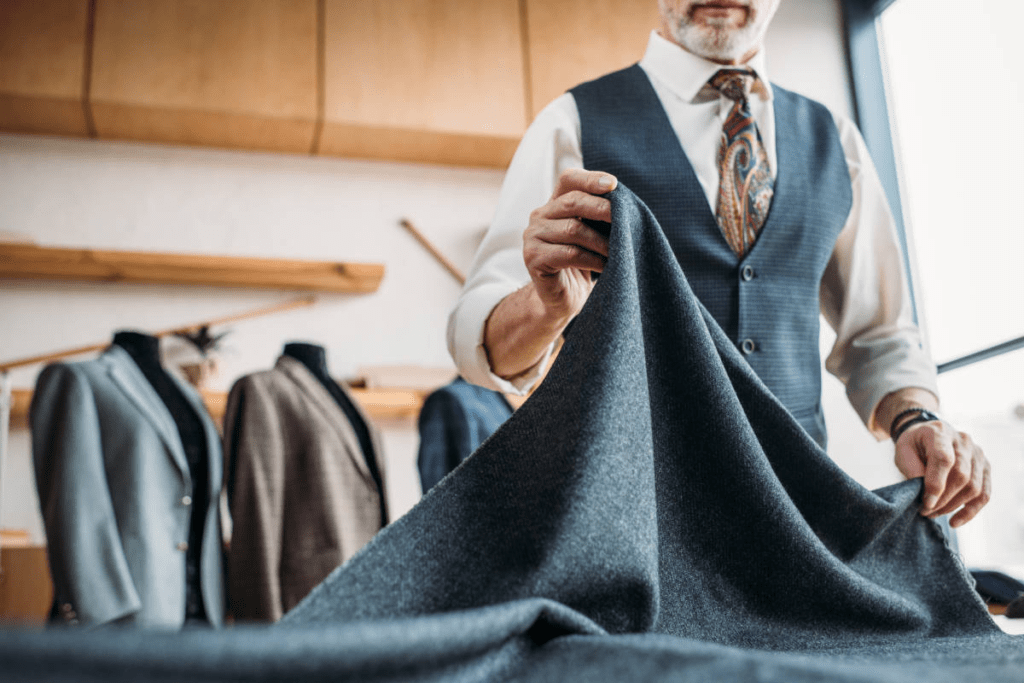
Now, I don’t want you to be put off by what I’ve just written. What I do I want to do is set realistic expectations. The amount of preparation work that you put into building the right foundations will ensure that you are able to move from draping physically to draping virtually without the kind of setbacks that could undermine the project as it progresses.
The good news is that many, if not all, of the 3D vendors have also been working very hard on helping to build these foundations. Companies like Browzwear, CLO 3D, Optitex, Gerber, Lectra, Romans CAD and others have been working on developing solutions to clearly define a materials characteristics. For the purpose of this article, I’ve picked out three examples of virtual draping put into practice, but keep in mind that most of the vendors listed in this article will use similar methods for material testing.
Browzwear’s solution, the Fabric Analyzer is one of the most advanced tools on the market. I actually travelled to Browzwear’s development centre in Israel back in the summer of 2017 to see the first physical material testing prototype. Once you’ve loaded the software, you then need to prepare each of the fabrics by ironing and removing any wrinkles to help provide accurate results. Before using the Fabric Analyser, fabric samples are cut into three separate lengths, along the length of the fabric grainline, then across the width and on the bias with each piece being 5cm x 30cm. Following this, the weight of the fabric, along with parameters such as fabric type (knit, weave, elastic etc.) and the fibre composition e.g. 90% nylon 10% elastane are entered into the testing software provided by Browzwear. The software then guides the user through the testing of the thickness and stretch of the material based off all three grain types – providing meticulously calculated physical characteristics for use in the 3D design environment.
CLO, another major player in the 3D sector, offers its own materials measurement tool in the form of the CLO Fabric Kit 2.0. They also follow the same method of cutting materials into three shapes and following similar processing. After measurements have been taken they can be entered into CLO’s design and specifically emulator tool, which allows the material to be simulated in an accurate 3D environment, providing designers with a clear understanding of the drape and fit of their designs.
CLO also offers a library of preassigned fabric properties that can be chosen from and combined with a material of choice. From this, the stretch, shear, bending, buckling, density, friction coefficient, damping and thickness of the fabric can be edited based on the designers needs through sliders in the software.
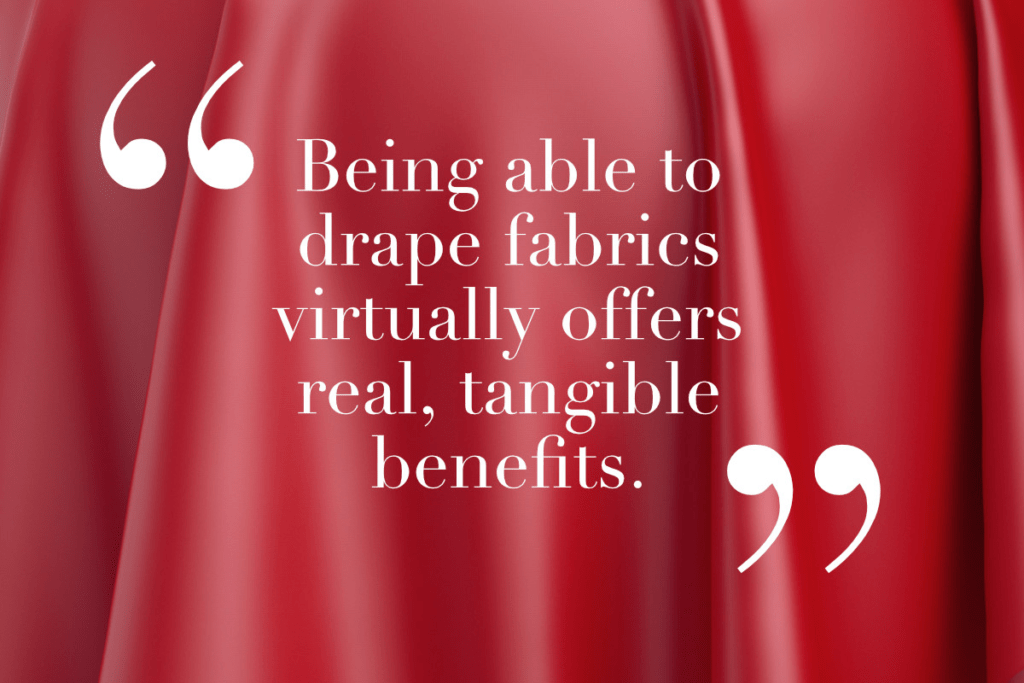
While not a tool specifically associated with apparel design, Blender is another 3D design tool that comes with pre-set fabric types allowing for simulation and could be used in the development of advertising materials or concept designs. The parameters around these pre-sets can be changed much like they can in the software offerings from Browzwear, CLO 3D and Optitex, however, the number of pre-sets is limited when compared to these other more specified vendors. Setting such as mass, air viscosity, tension, shear and compression can be edited with material pre-sets such as silk, cotton and denim.
As stated in my first article on the subject of material scanning, it’s critical that you consider the use-case carefully. If the purpose is to create internal prototypes then the scanning resolution can be lowered, resulting in quicker turnaround times, but if you want to use the scanned material to design and develop photorealistic virtual-twins, then your resolution settings must be set to ultra-high.
Now, assume that we have scanned the materials linked to your chosen use-case, then the next step is to measure the materials physics carefully, to help ensure that you achieve the best possible virtual draping. A solution which offers a wide range of predefined material pre-sets may suit your use-case or you may require a more complex workflow in which you can analyse and import each individual fabric to achieve the closest results to those of the real world, over time experience will play a key part of the process best-practice.
Being able to drape fabrics virtually – whether it’s for prototyping, sampling, or production – offers real, tangible benefits. And on the whole, 3D design and development solutions offer high-fidelity results – provided they are passed material files that originate with scanning at the right resolution for whatever use case you have in mind.
Across the 3D sector, innovation is at an all-time high, and demand from customers – spurred on by the COVID-19 pandemic’s massively disruptive effect on global supply chains – is also unprecedented. Together, these forces will, I hope, lead to a world where the virtual can emulate the physical more closely than ever – with compounded benefits everywhere in the value chain.